碳酸氢钠超微粉磨机
我公司根据SDS干法脱硫工艺中所喷射的碳酸氢钠超微粉脱硫剂要求,吸收国外先进磨机制作经验,研发了新型碳酸氢钠超微粉专用磨机。该设备占地面积小,噪音低,磨粉粒径超细,合格率高,故障率低。
磨机系统说明:
1). 该机是一种卧轴(立轴)反射型粉碎机,能同时完成微粉碎和微粒分选两道加工工序,粉碎机由动盘及齿圈组成,通过特殊形状的动盘高速旋转,物料颗粒在动盘及静止齿圈之间反复多次受到挤压、碰撞、剪切,从而达到粉碎,由定量喂料系统把物料输送到粉碎腔内,物料在高速旋转的转子与齿衬的定子之间受到冲击和剪切,粉碎后的物料在气流的带动下进入分级区,合格的物料通过旋风和除尘器收集,不合格的物料重新返回到粉碎区进行粉碎。
2). 机结构紧凑合理、体积小、耗能低,效率高,转动平稳,噪声低,密封可靠,无粉尘污染,安装简单,易拆易修,调换损件方便
3). 该设备采纳国内外干法机械粉碎机的特长,根据需要可采用大风量入腔或水夹套冷却,以降低粉碎热量,防止物料颗粒粘壁、粘粉碎盘面的弊病。。
4). 粉碎、分级一体机,能将达到细度要求的物料及时分送出来,避免过粉碎,物料粒度分布窄。
5). 适合加工各行业的多种物料,在不停机的情况下,可任意调节粒度。产品粒度均匀,细度可达1um
6). 本机应用广泛,适用于莫氏硬度小于8,含水量小于10%的干性物料都可以采用本机粉碎。
7). 对于团聚物,有很好的打散和分散功能,带有自动排渣、不易粉碎物功能
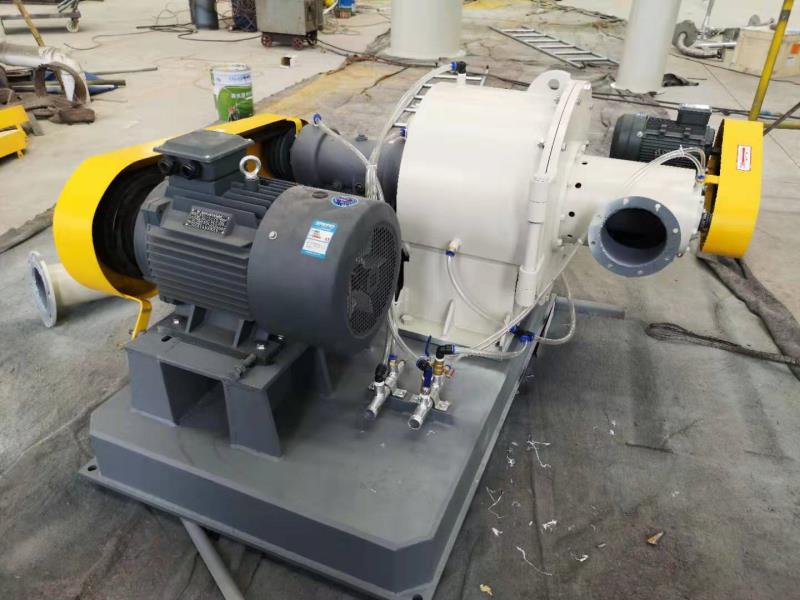
超频振动膜设备
我公司根据SDS干法脱硫工艺中所喷射的碳酸氢钠超微粉脱硫剂要求,吸收国外先进磨机制作经验,研发了新型碳酸氢钠超微粉专用磨机。该设备占地面积小,噪音低,磨粉粒径超细,合格率高,故障率低。
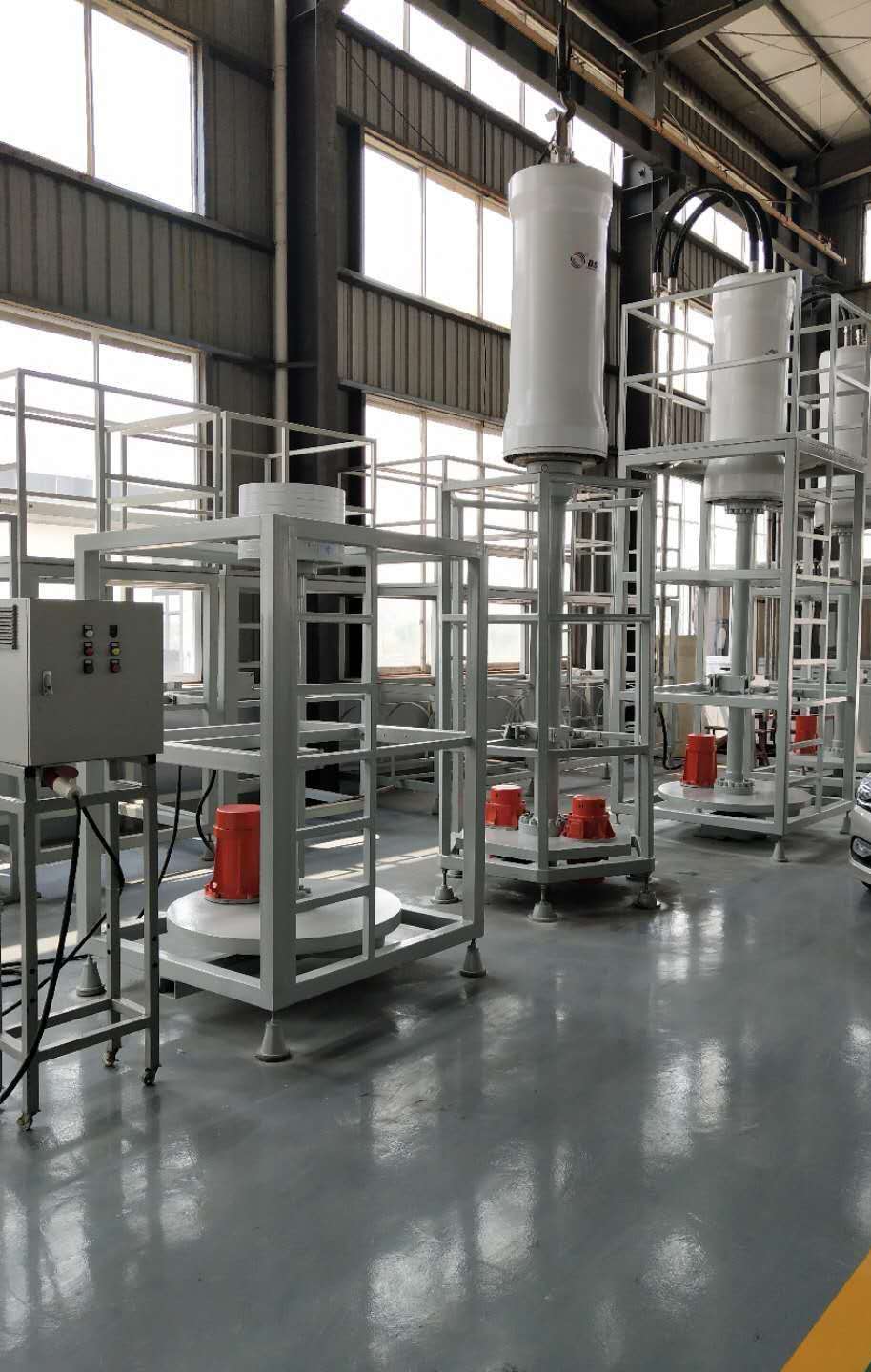
莽野防腐涂料
公司自主研发的特种无机聚合物为成膜物,以高度分散活化的钝化金属微粒、纳米石墨鳞片、纳米金属两性氧化物、超细稀土超微粉体等功能物质作为防腐填料。涂料颜色为灰色或黑色具有优异的防物理腐蚀、化学腐蚀、电子腐蚀性能。本产品可在不高于400℃的高温环境中长期使用,产品对环境无污染是符合环保要求的环境友好型涂料且具有超强附着力,耐磨耐冲击,施工简单方便等优质特性。
适用行业:石油化工重工业防腐、沿海钢结构防腐、污水处理设备防腐。
炼钢厂、火电厂、垃圾焚烧、焦化、脱硫脱硝、酸碱储罐、烟囱管道、脱硫塔、船舶等高防腐要求的内壁。
脱硫塔内壁,脱销设备内壁,预热器内壁,氨水储罐内壁,垃圾渗滤液收集斗,酸洗工艺钢段。
酸洗工艺钢段、盐酸再生钢段、烧结烟气风筒、冲渣处理段、高炉煤气管 道内壁、原料储罐内壁、柴油罐内壁、污水池内壁、垃圾渗滤液 USB 池、MBR 池、工业机械设备等涉及到的强腐蚀部位。
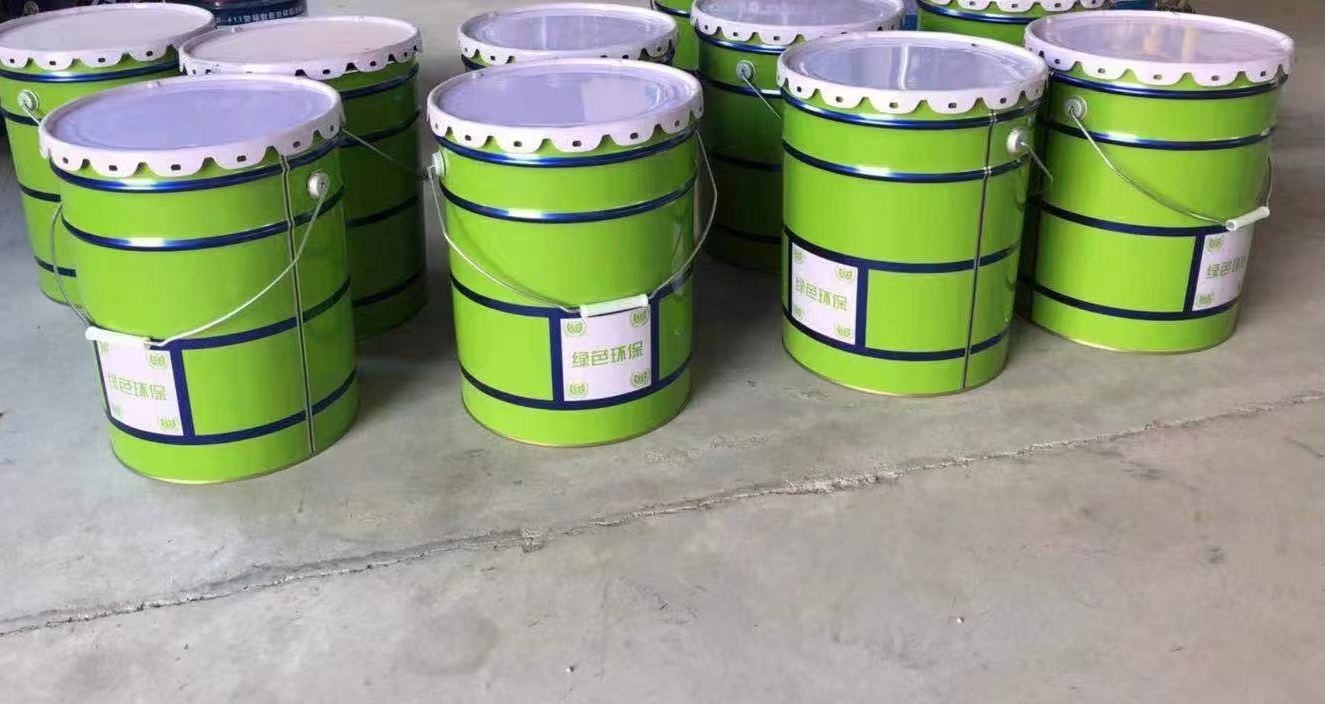
高活性钙脱硫剂
产品型号:TL001-SDS
其他类似关键词:SDS活性钙脱硫剂、高活性钙脱硫剂、高活性钙基脱硫剂、活性钙脱硫剂、SDS干法脱硫剂
SDS钙基干法脱硫剂是一种可以替代碳酸氢钠、小苏打超微粉的干法脱硫剂,用户无需使用磨机,烟气温度范围更加宽泛,而用量和效果不变,具有减少附属设施、清洁智能操作、降低运行成本、废物合规处置等优势,可以从根本上解决钠基脱硫副产物处置难题,是企业降低脱硫成本的不二选择。
国内普遍以小苏打(碳酸氢钠超微粉)作为脱硫吸收剂,价格太高无法满足低碳低成本要求,上世纪九十年代,日本和欧盟率先开发出了高活性氢氧化钙,并成功替代了小苏打,应用于烟气脱硫领域。
目前,我司已研制并批量化生产出“莽野”品牌的高比表面积、高活性的sds钙基干法脱硫剂,它是通过特殊工艺加工制造而成,从颗粒结构上具有大量空穴、褶皱形态,从而区别普通氢氧化钙产品。 因此,在气体吸附、反应活性、反应速度、产品利用率及流动性上具有无可比拟的优势,使用布袋除尘器可高效捕捉,有效延长脱硝催化剂寿命,且钙基脱硫副产物,可广泛应用于建材行业,便于资源利用。使用后脱硫运行成本大幅降低,满足企业节能降耗的要求。
国内钢铁、焦化企业均已建设烟气脱硫脱硝装置,多数企业选择碳酸氢钠/小苏打作为烟气干法脱硫的脱硫剂,脱硫副产的可溶性钠盐混合物回收利用率低,甚至无法利用,造成大量工业固废堆积,增大了二次环境污染风险。高活性钙基脱硫剂替代小苏打,可广泛应用于建材行业,解决了固废无法利用的难题。
使用高活性钙基干法脱硫剂现场图片:
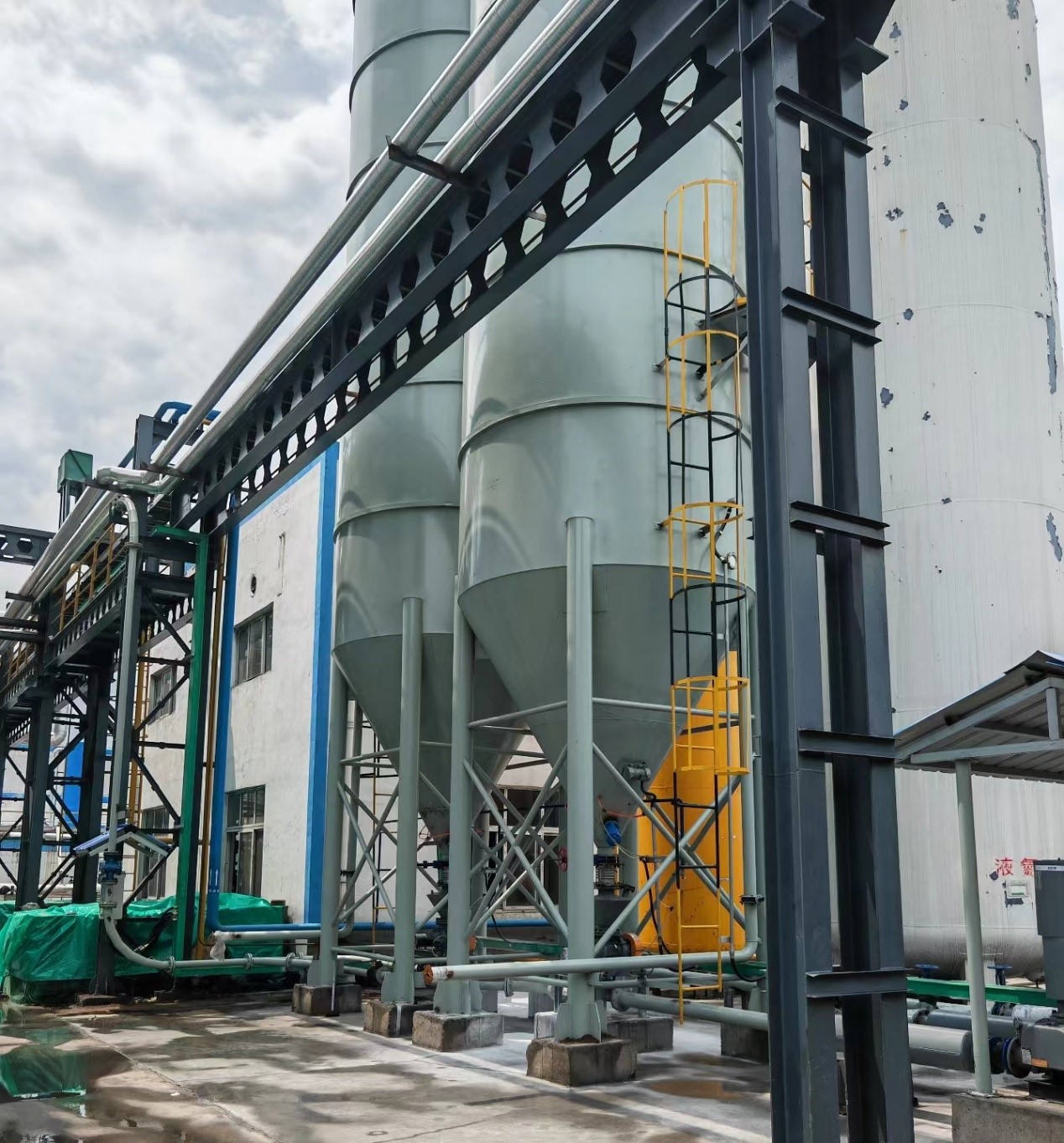
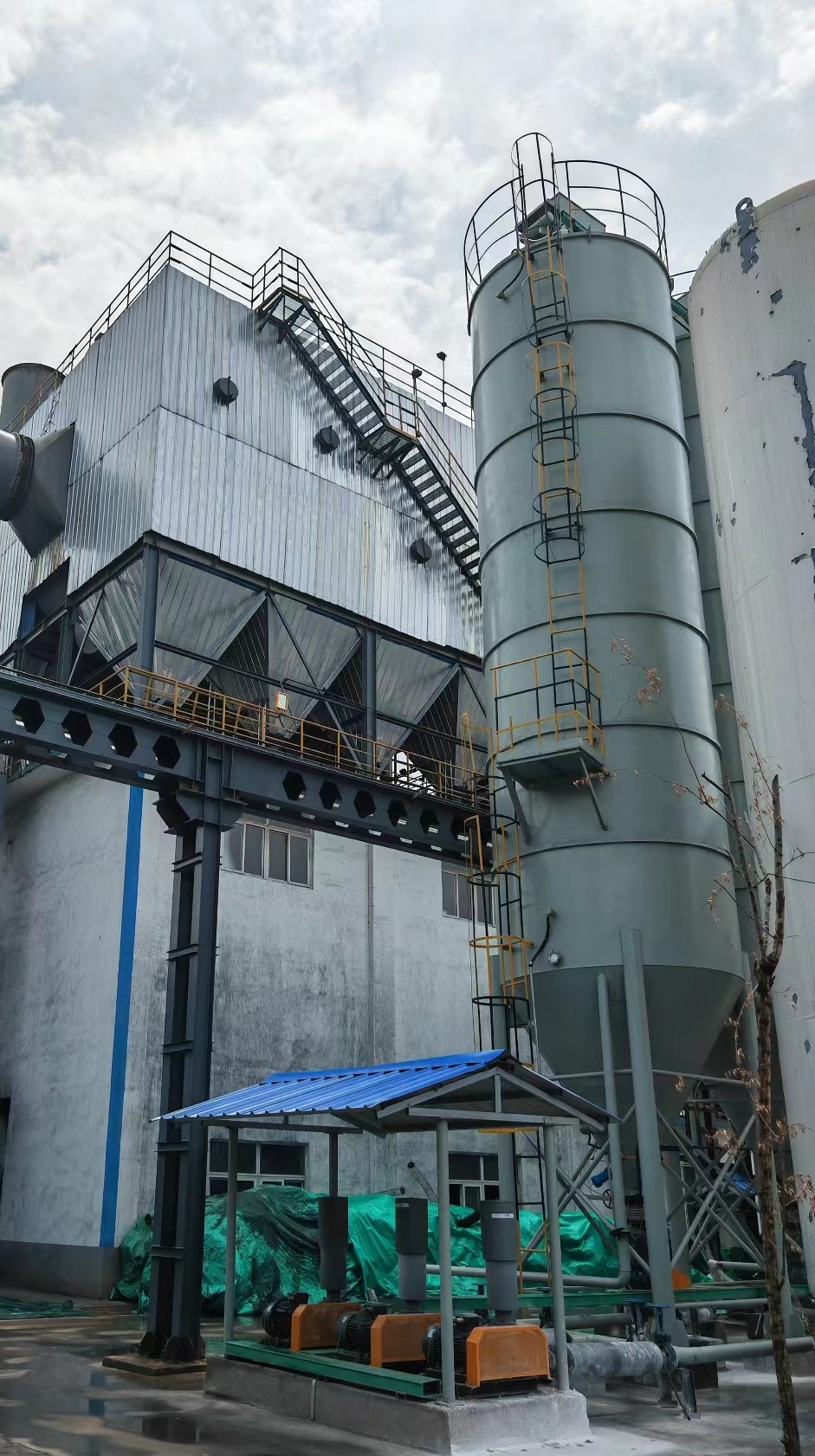
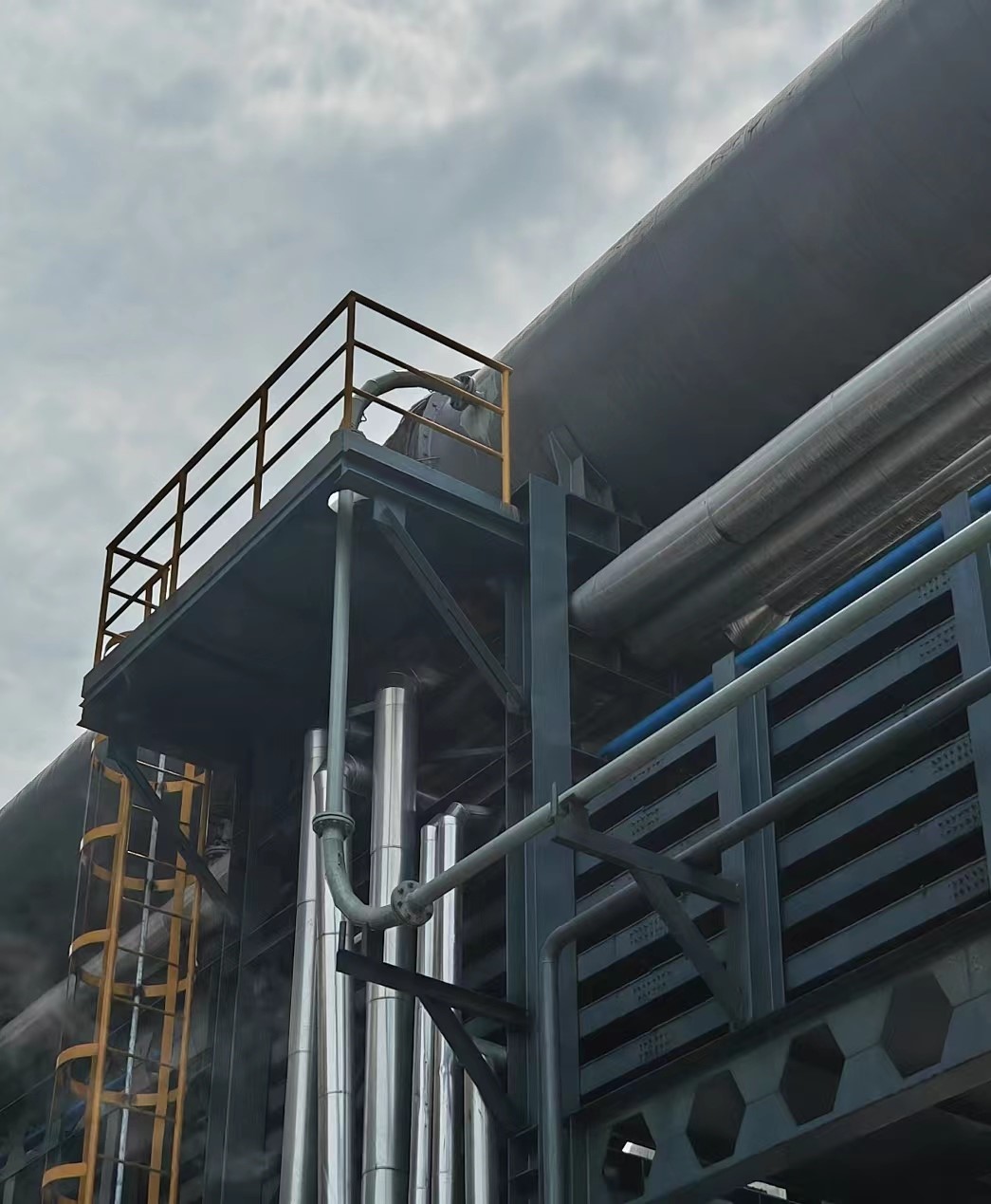
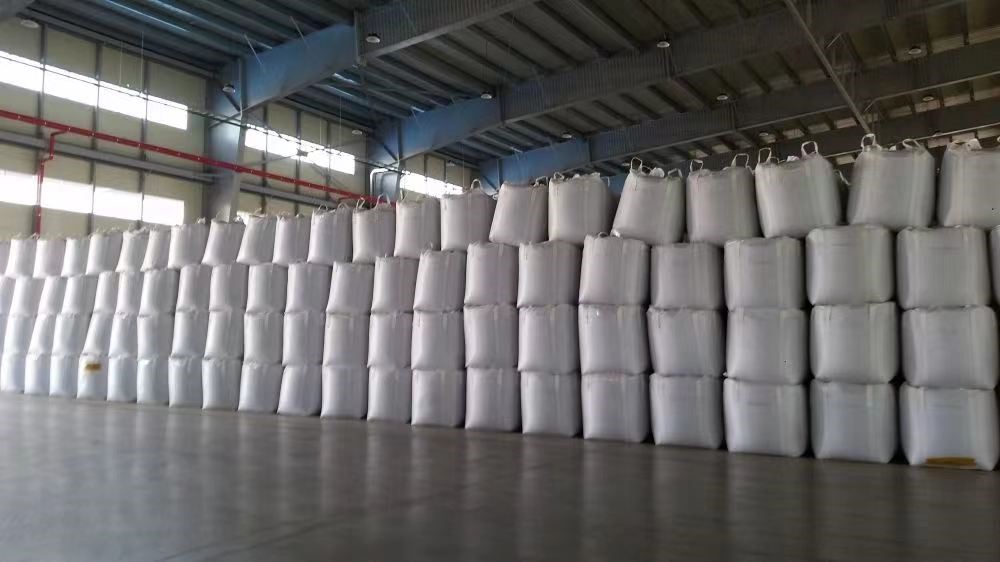
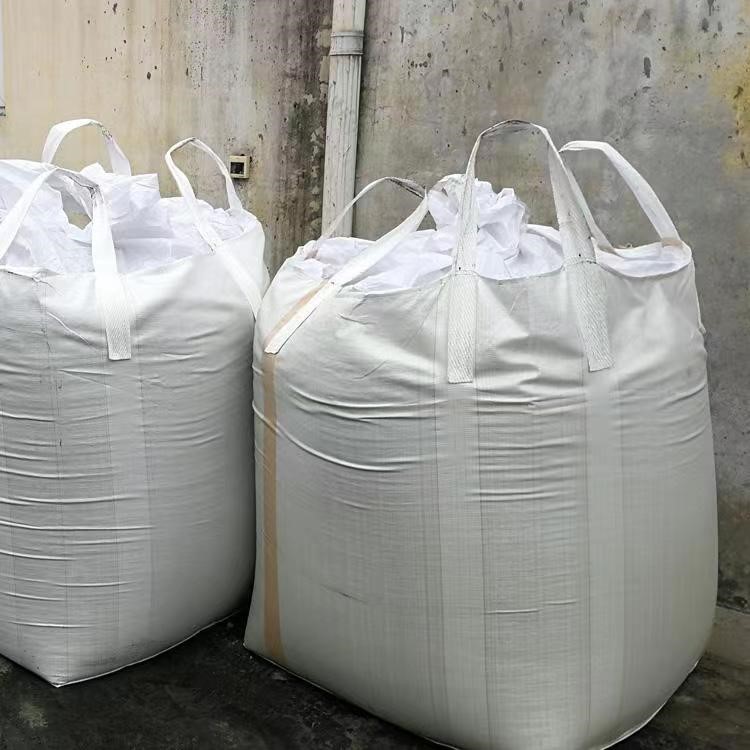
脱硫浆液活化剂
产品型号:TL002-SHI
其他关键词:高效脱硫添加剂/脱硫增效剂/脱硫提效剂/湿法脱硫助剂
上海莽野环境技术有限公司针对石灰石(石灰)-石膏湿法脱硫系统,专门研发了“莽野”牌高效脱硫浆液活化剂,用以改善石灰石浆液与S02反应的边界条件,强化其脱硫过程,提高脱硫反应速率及效率,拓展脱硫系统对燃煤含硫变化的适应能力,在确保烟气S02 达标排放的基础上,可以大幅降低能耗。该产品已在国内湿法脱硫系统得到广泛应用并取得了良好的经济和社会效益。
药剂原理如下:
脱硫浆液活化剂是针对提高石灰石(石灰)-石膏湿法脱硫系统处理能力,而开发研制的由复合多元酸、磷酸基高分子化合物等组成的固体粉剂。其中主要包括碳酸钙促溶剂、表面活性剂、氧化催化剂、pH值缓冲剂、缓蚀阻垢剂,其主要作用如下:
- 通过碳酸钙促溶剂,促进碳酸钙的快速溶解,为脱硫反应提供充足的Ca2+,是提高脱硫反应速率的前提;
- 通过表面活性剂降低SO2传质过程中双膜阻力,提高脱硫系统对SO2的吸收速率, 快速将气相SO2以亚硫酸根的形式储存在液相中;
- 通过氧化催化剂提高液相中亚硫酸根的氧化速率,将亚硫酸根转换为稳定性更高的硫酸根,硫酸根与钙离子在液相中反应生成石膏排出脱硫塔;
- 具有pH缓冲作用,为脱硫反应提供稳定的操作空间;
- 具有缓蚀阻垢作用可保证脱硫系统长周期稳定运行。
我公司高效脱硫浆液活化剂的产品优势如下:
- 用量低。可根据实际工况调整;
- 使用方便。无需额外的加药设备,直接通过地坑投加,搅拌溶解后通过地坑泵注入吸收塔内;
- 起效快。脱硫浆液活化剂溶液进入吸收塔后,5分钟内便有明显的效果。
我公司产品给用户带来的好处如下:
- 可以提高燃煤硫份,降低燃煤成本。工况保持不变的情况下,添加脱硫浆液活化剂后燃煤硫份提升20%-30%后仍可确保环保达标,单台脱硫系统每年可产生百万以上效益;
- 可以停泵节能,降低脱硫电耗。通过使用脱硫浆液活化剂提高脱硫反应速率,可实现较低液气比的情况下脱硫效率保持不变,在相同工况下可多停运一台浆液循环泵,同时可降低引风机电流、节省检维修费用,单台脱硫系统每年可产生几十万以上效益;
- 降低SO2排放量,解除环保压力。通过使用脱硫浆液活化剂提高脱硫效率,降低SO2 排放量。
应用案例:
案例一:
国电湖北某电厂2x660MW机组脱硫系统,一炉一塔,均为石灰石-石膏湿法烟气脱硫工艺,设计脱硫塔SO2入口浓度3425mg/Nm3,浆液循环泵4台,功率分别为 900/1000/1100/1200KW。脱硫系统需运行4台浆液循环泵才能使得SO2出口浓度达标(排放标准 35mg/Nm3)。
脱硫系统系统投用脱硫浆液活化剂并维持10OOppm浓度,入口SO2浓度稍有提升的工况下,系统只需运行3台浆液循环泵即可使出口SO2浓度达标,且出口浓度相较加药前还稍有降低。
节能效益:
投用脱硫浆液活化剂后吸收塔停运一台浆液循环泵,停泵功率1000kw/h,电价为0.32 元/kw。
泵停运一天可节约电费:1000kw/hx24hx 0.32=7, 680元
每月节省电费:7680x30=230, 400元
以上还没有计算引风机电流下降产生的效益。
系统适应燃煤硫分的能力变强。系统在使用脱硫增效剂后,可以明显提高脱硫效率和系统处理能力。在保持相同效率的前提下可以提高系统燃煤硫份30%左右。高硫煤的价格 要略低(每吨差价可达20-40元左右),提高高硫煤掺烧比例,可降低电厂的购煤成本, 此项经济效益可达上千万元。
应用案例二:
江苏某开发园区热电厂,2xl5kW热电机组,两炉一塔,采用石灰石-石膏湿法脱硫, 执行超低排放,原烟气SO2浓度1700mg/Nm3,循环浆液泵运行3台,功率均为280kW, 钙硫比可达1.20,粉耗居高不下。
使用脱硫浆液活化剂并维持10OOppm浓度,仅2台泵运行即可排放达标,而且粉耗下降了 17%,钙硫比稳定在1.03以内。
节能效益:
停运泵电流370A,增压风机电流下降20A,电压380V,电价0.5元/度,月节省电费:
1.732 x 0.85 x (370+20) x 0.38 x 24 x 30 x 0.5 = 78, 545 元
粉耗下降17%,每月节粉180吨,单价170元/吨,月节省粉费:
180x170=30, 600 元
每月效益合计:78, 545 + 30, 600=109, 145 元
以上不包括停泵节省的检维修费用及设备维护费用。
应用案例三:
四川某钢铁集团200万吨烧结球团石灰石-石膏湿法脱硫系统,原烟气SO2浓度 4800-6800 ( mg/Nm3),脱硫效率大于98%,钙硫比小于1.03。当入口烟气SC^浓度 5800mg/Nm3以上时需开启全部5台浆液循环泵,当入口烟气SO?浓度6500mg/Nm3以 上时随时有超标危险(净烟气SO?浓度小于200mg/Nm3),环保压力巨大。
浆液添加活化剂并维持浓度1000ppm,当入口烟气SO?浓度6800mg/Nm3以下时, 在停运次大泵的情况下满足了超低排放标准(净烟气SO2浓度小于35mg/Nm3)
节能效益:
同样条件下减少了 1.5台泵,停运电流达到45A,同时停泵前后引风机电流下降 2.5A,电压均为10kV,每月30天,用电0.6728元/度,烧结球团脱硫系统每月省电费: 1.732 x 0.85 x 10 x (45 + 2.5) x 24 x 30 x 0.6728 =338, 750 元
另外如提升铁矿含硫量从而降低原材料采购成本,每年可增效1500万元以上。
以下是使用高效浆液活化剂的石灰石石膏工艺现场图:
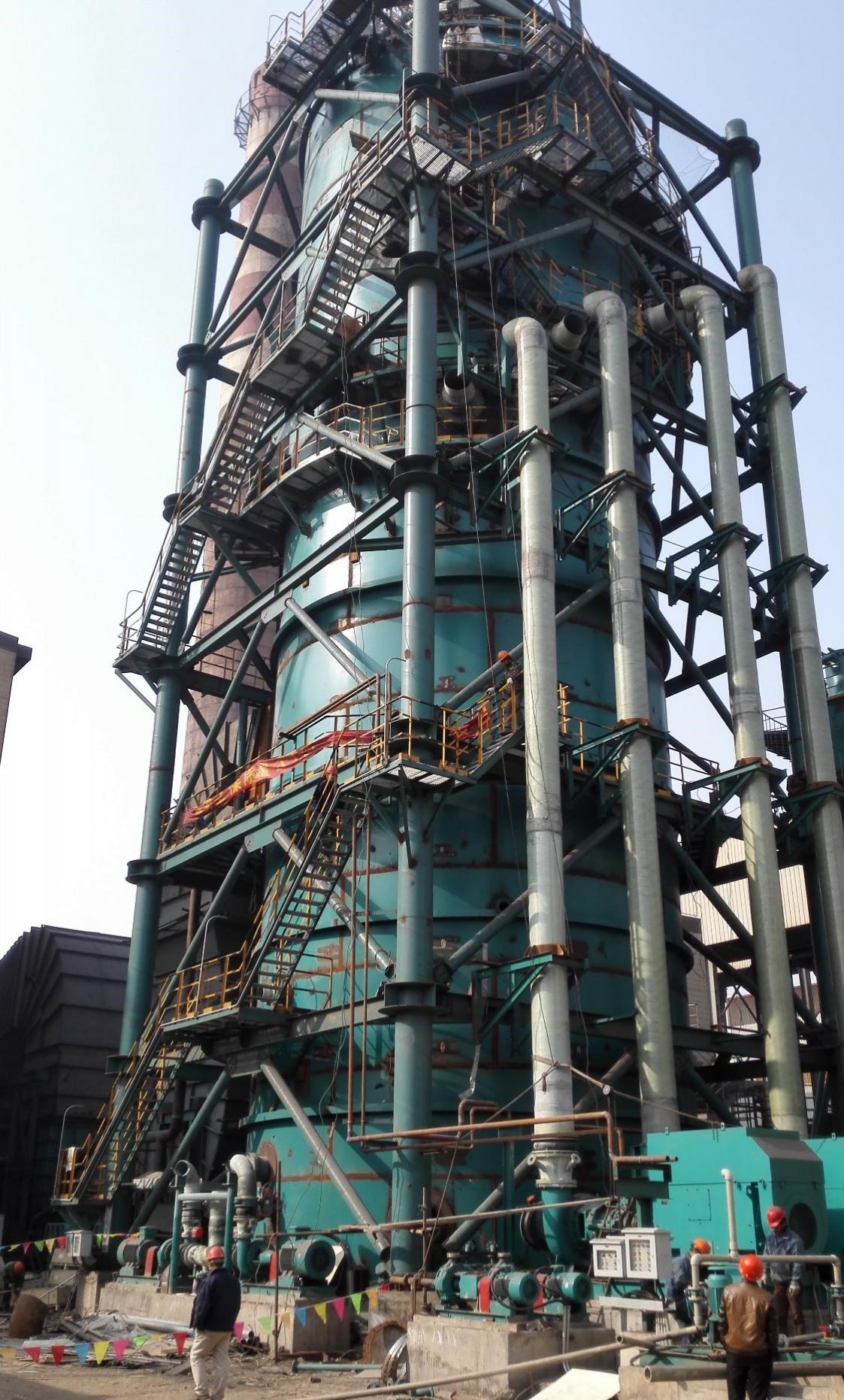
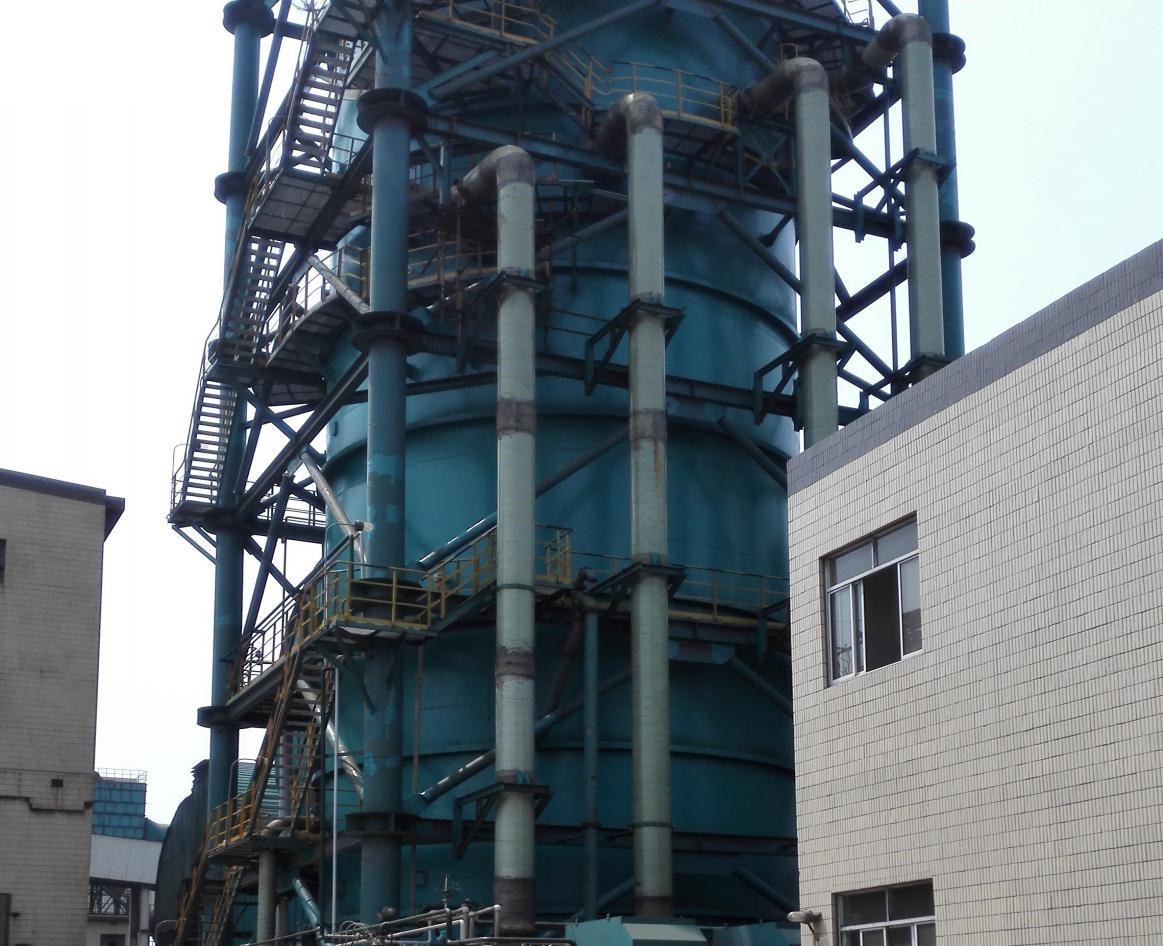
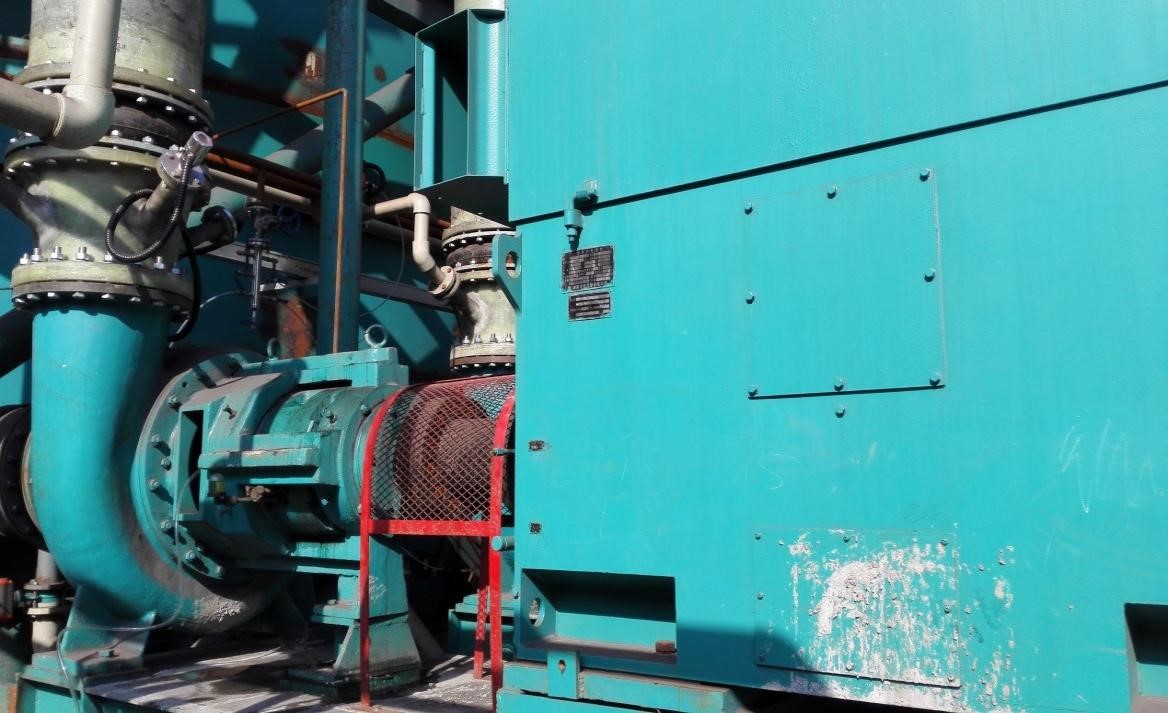
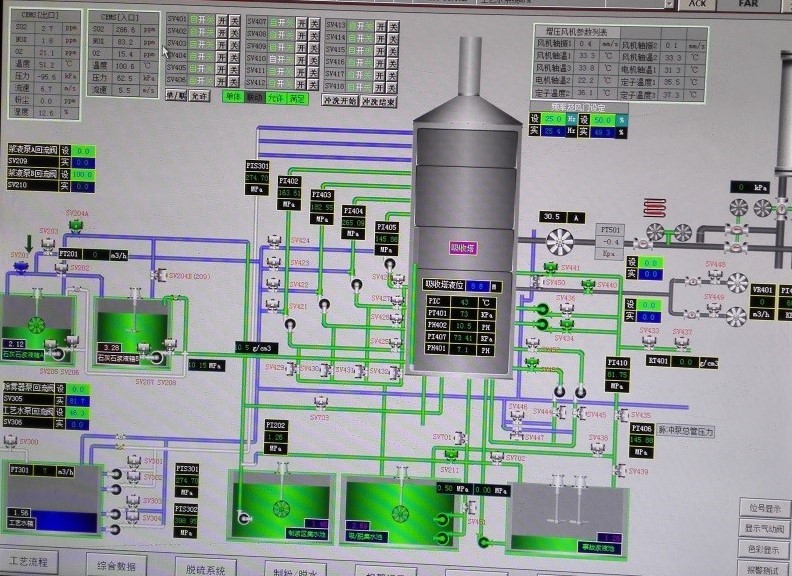
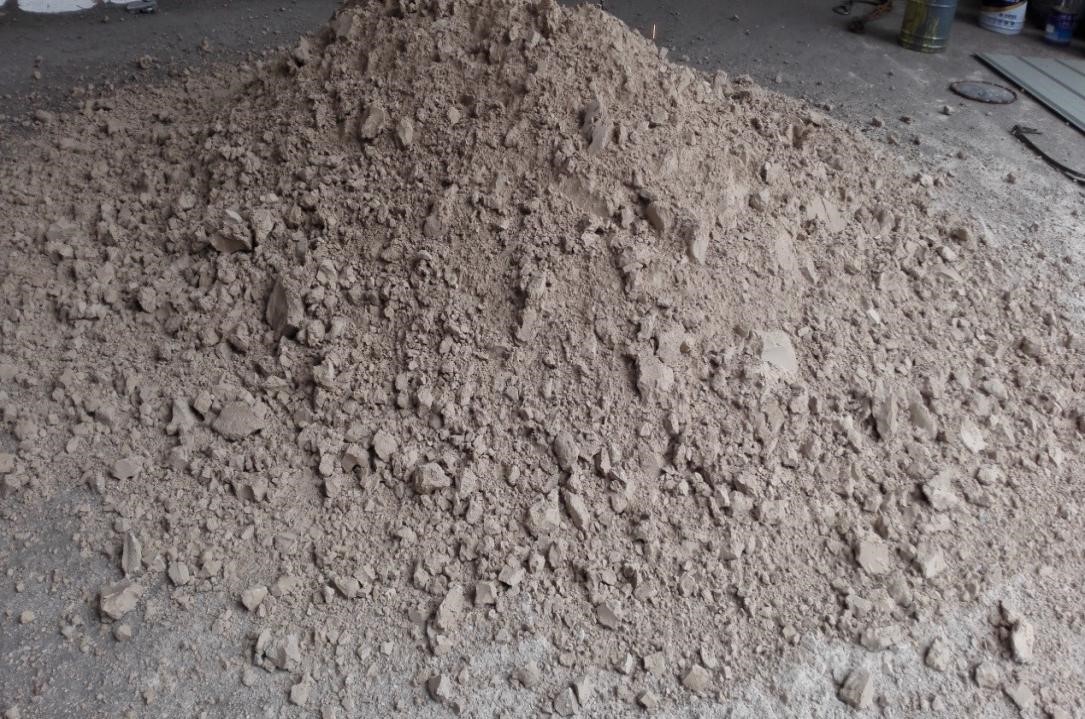
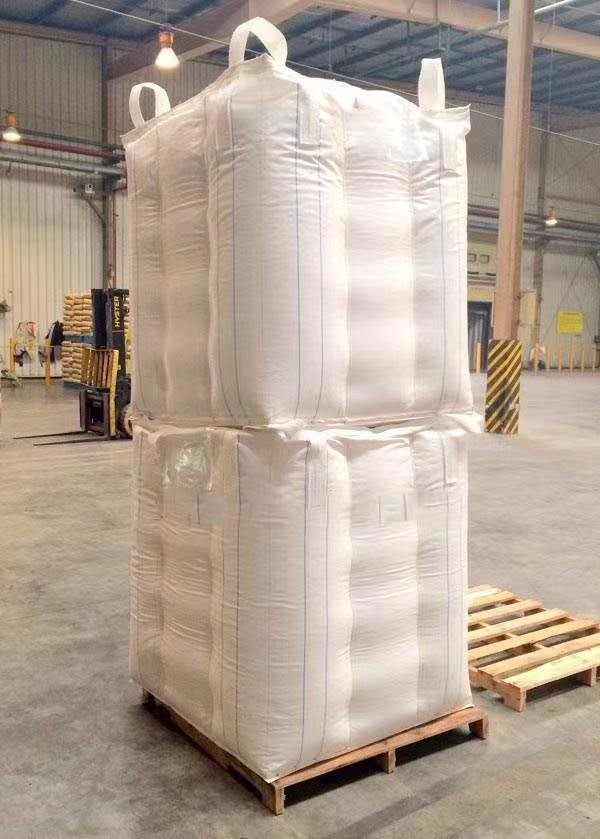
生物质脱硝剂
生物质脱硝剂BDA(biomass denitration agent)是一种有别于传统的炉内还原脱硝剂(如氨水和尿素等),具有较高的脱硝效率,无腐蚀性,不会造成氨逃逸。产品为液体药剂,无特殊气味,冰点低:-16℃ ~ -18℃,密度:1.06-1.19,主要成分为有机活性物、大分子长链有机质等。采用罐车或者液袋运输。
生物质高效脱硝剂脱硝原理:
有机活性物、大分子长链有机质等在500℃以上的高温下快速裂解成小分子游离态生物质自由基团,即裂解生成CO和碳氢自由基等,其催化还原能力高于氨基脱硝剂,将一氧化氮还原成无害的氮气,达到脱硝的目的。
反应步骤如下:
第一步:高温裂解产生自由基和还原剂
第二步:NOX还原成N2
CO+NOX —— CO2+N2 CnHm*+NOX—— CnHmO+N2
生物质高效脱硝剂的优点:
- 不需要对锅炉进行大的改造,不用催化剂,不产生固体废料;
- 气化生物质脱硝剂能与烟气充分混合,反应迅速,脱硝率高。适应温度区间500--1100度;
- 不需要还原剂的加热溶解过程,自动化程度高;
- 脱硝系统运行安全卫生;
- 炉温度符合生物质脱硝液合适的反应温度和反应时间;
- 对锅炉正常运行无影响,无腐蚀。
低温脱硝剂
低温脱硝剂(LDA)是一种有别于传统的氧化法脱硝剂(亚氯酸钠、次氯酸钠)的低温还原法脱硝剂。是真正能在常温或低温条件下将氮氧化物还原成氮气的脱硝药剂。使用方法是在脱硫塔后面的脱硝装置内循环喷淋使用。相对于氯基氧化法脱硝和臭氧法脱硝工艺,具有运行成本低、高效稳定,没有二次污染的优点。
本低温脱硝剂为液体,采用罐车或者液袋运输。
除尘催化剂
除尘催化剂(DRC)是一种加在脱硫脱硝循环水池溶液中的除尘添加剂,起到催化、溶胀、锁定超细颗粒粉尘的作用,可以使烟气中的颗粒物应收尽收,无处遁形,可以替代湿电除尘器,达到粉尘超低排放的效果(<5mg/Nm³)。
本品为易溶于水的固体粉末,25公斤/袋装。